KATO® inserts are offered in Tanged, Tangless®, and various materials and surface finishes.
Materials include stainless steel, Nimonic 90, Nitronic 60, Inconel X750, Phosphor Bronze, and more. Our standard range offers options like Cadmium plating, Silver plating, and Lubricated finishes.
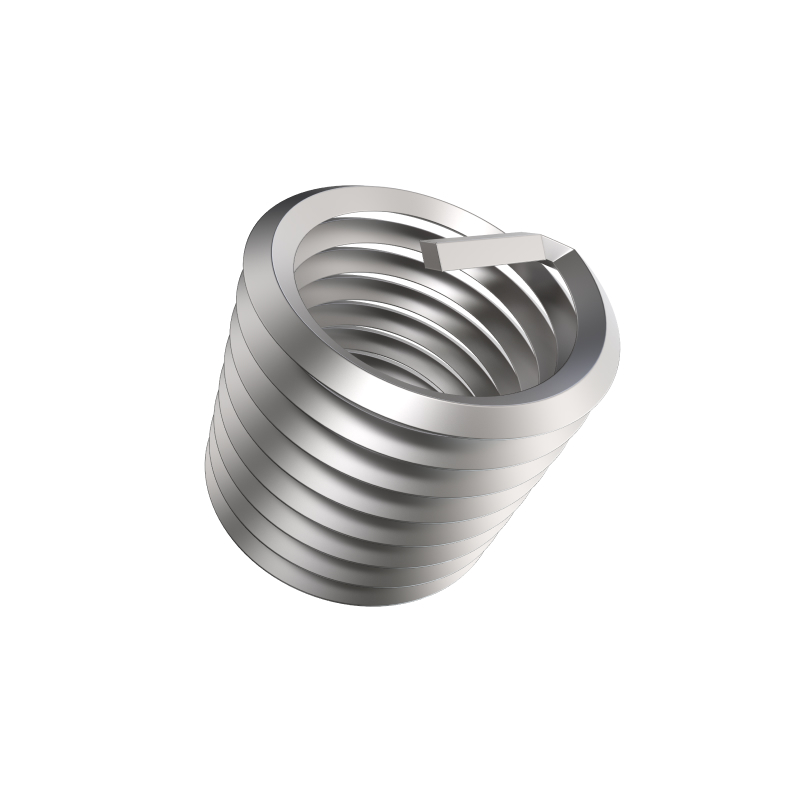
KATO® Tanged Inserts
- The original wire thread insert. Originally created in Japan, and used throughout the world in applications as diverse as automotive and aerospace, to consumer electronics and robotics.
- A history of excellence, a product of innovation. We have continuously improved, refined and iterated upon since the 1980s. KATO inserts are created using new wire-cutting techniques, new materials and comprehensively coated with innovative surface finishes.
- Made in every conceivable size, unified and metric, in a plethora of materials.
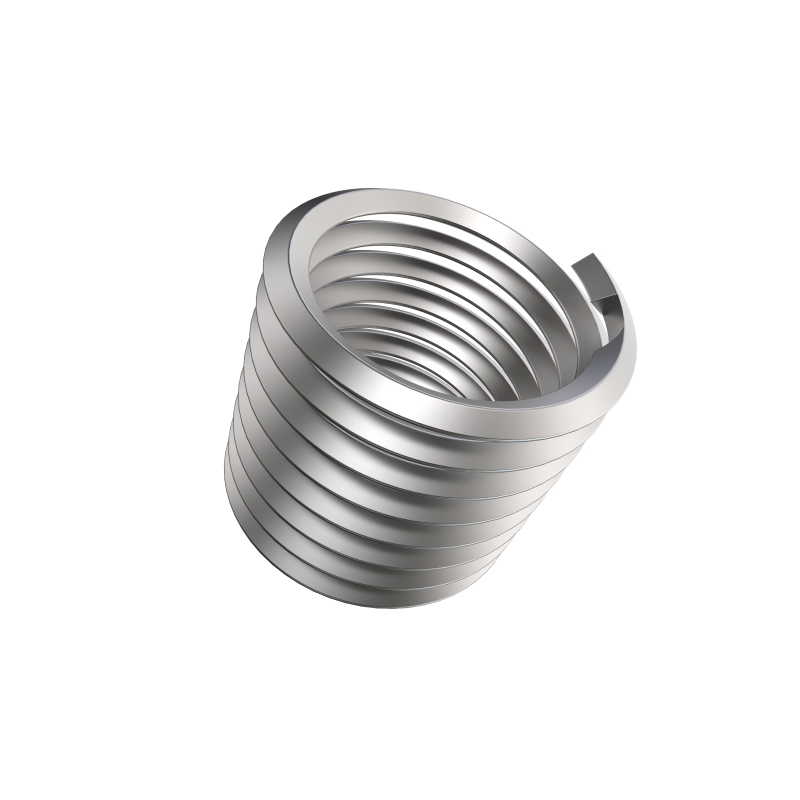
KATO® Tangless® Inserts
- Tangless® wire thread inserts are slowly becoming the first-choice of wire thread insert across every high-volume manufacturing industry.
- Without a tang, these inserts eliminate all risk of foreign object debris (FOD), but also make them re-usable and more sustainable.
- Widely available, in unified and metric sizing, in the same variety of materials and surface finishes as KATO® tanged inserts.
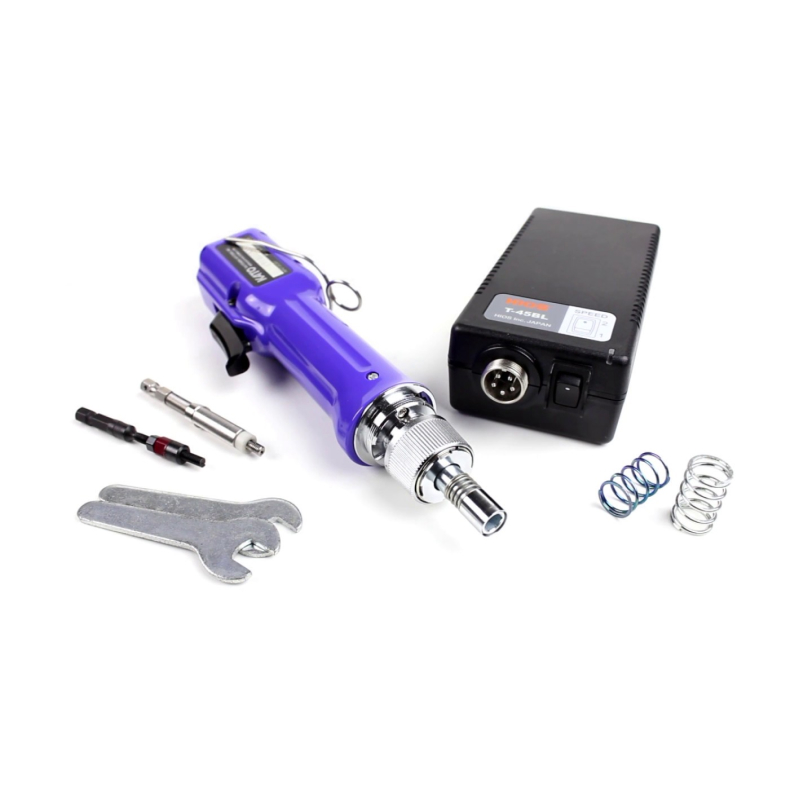
KATO® Tooling
- Our dedicated KATO® tooling speeds up installation times, for everything from high-volume applications to one-off disassembly.
- Tooling available for all manufacturing setups and for assembly of all types of equipment; from manual hand-tools to torque-arm and automatic power installation tools.
- Built to perform. We provide expert training and continuous support for manufacturers of all kinds.
Our Industries
KATO® wire thread inserts are used extensively across industry. We’re proud to support world-class manufacturers in their efforts to improve the performance, quality and viability of their products.
Want to discuss your requirements?
Why choose KATO®?
Quality
Crafted by purpose-built machinery, inspected individually by our experts. KATO® products are made in medical-grade production facilities, to automotive, aerospace and internationally recognised quality management standards.
Speed
Our operating principles are guided around speed, ensuring manufacturers have product-in-hand just in time. The unique product design that KATO® users have come to know enables quick installation, all while increasing joint strength.
Innovation
KATO® wire thread inserts are the most innovative on the market. Through decades of continuous improvement and product development, KATO® Tanged and Tangless® inserts enable lighter, stronger designs that last longer.
Value
KATO® offers exceptional value to manufacturers. With competitive pricing, short lead times, and a full range of metric and unified sized solutions, we’re able to provide market-leading value to customers.
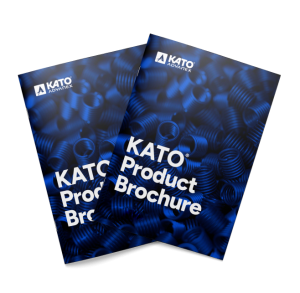
Get KATO® Pricing, Lead Times and Order Now
Speak to our team of experts who are here to help.